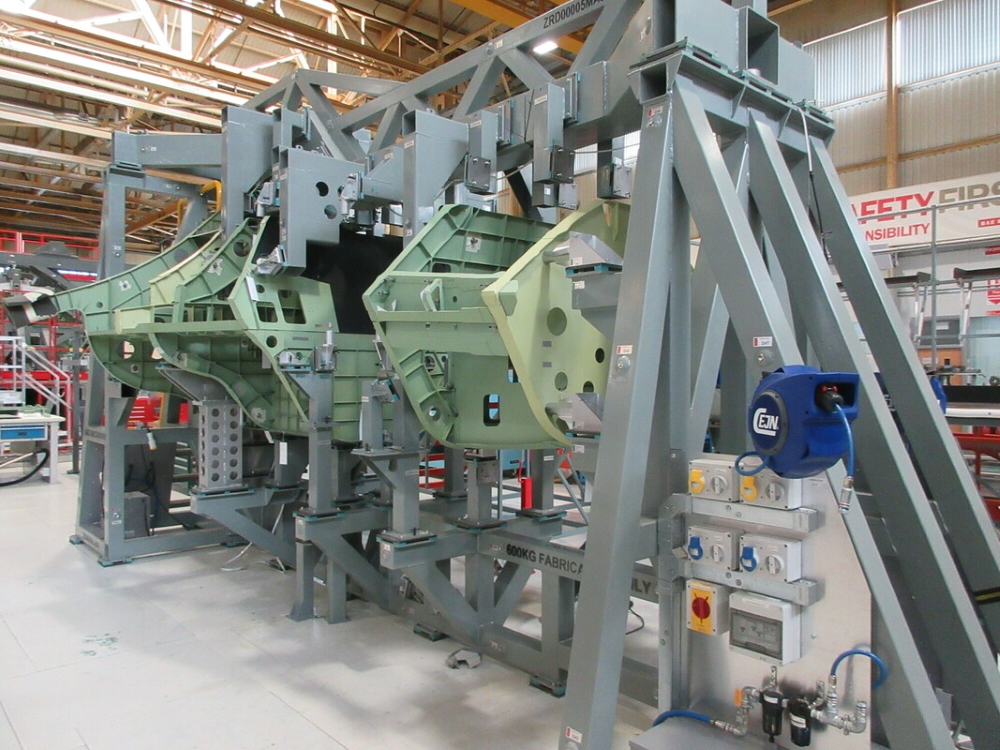
Work continues as planned to prepare a supersonic TEMPEST demonstrator for flight by 2027. At Farnborough, BAE Systems revealed that more than 50% of the weight of the new aircraft is already in production at Samlesbury, the same factory that is already involved in "stealth" since for many years now it has been producing empennages and rear fuselage sections for the F-35.
All of the major structural units are in build, and the process is putting to the test the “factory of the future” concept by utilizing novel and advanced technology and techniques, from the use of augmented reality to help the workers to digital rigs all the way to new manufacturing methods.
Air Commodore Martin Lowe, Future Combat Air Systems Programme Director for the UK Ministry of Defence has explained that, while the demonstrator will not be fully representative of the final design for TEMPEST/GCAP, it will be fundamental to live-test key features and to understand more about the advanced technology that is required to deliver a sixth-generation fighter jet.
The demonstrator will have stealth features including a working internal weapon bay and S-shaped air ducts. It will however use EJ200s, the engines of the Eurofighter TYPHOON, as its propulsion system, rather than the new engine eventually destined to power GCAP.
BAE Systems is working with more than 100 UK supply chain partners for the build of the demonstrator. Already in 2022 it had showcased a demonstrative fuselage section which had been developed validating new robotic assembly machinery and techniques, additive manufacturing, augmented-reality assistance to the assembly and friction stir welding.
Some 20 different patents were generated from those early activities. Additive manufacturing processes, including 3D printing, is a key part of the build. Another advanced technique in use is Hot Isostatic Press (HIP), which employs extreme heat and pressure to create a solid metal part in any required shape. HIP is faster and cheaper than traditional forging methods and creates less material waste.
BAE says that some lead times have been reduced from 2 years to as little as 6 months. Development of the demonstrator with first flight planned for 2027 was first announced in July 2022. During 2023, key progress had already been reported, in particular with the demonstration on a rig in Filton of EJ200 functionality with the new stealth air ducting and diverterless supersonic inlet. A modified Martin-Baker Mk. 16A ejection seat (itself also operational on TYPHOON) was sled-tested, while bespoke simulators and rigs were used to allow pilots and engineers to test out early the various new features of the jet.
TEMPEST / GCAP will be a very large aircraft, built for carrying a large internal payload over great distances, and the demonstrator will be much larger than the TYPHOON. The air ducts are reportedly 10 meters long, to which the length of the EJ200 must be added. This means that the demonstrator will be, from air duct to engine nozzles, as big or indeed longer as an entire TYPHOON. Prospective pilots have already flown more than 215 hours on the bespoke simulator.
Inside Hangar 5 at BAE System’s Warton plant, 4 key integrated development rigs are known to be in use: one for the cockpit, one for flight control system management, one for computing and models, and one for the utility management system. From what was said in 2023, the cockpit uses a sidestick rather than a central column like on TYPHOON. This will ease use of a large panoramic display.
The final cockpit for TEMPEST / GCAP will probably be even more advanced. In the meanwhile, 2Excel is making progress on readying the EXCALIBUR flying laboratory, a modified Boeing 757, for its first flight. EXCALIBUR is being modified with bulges, fairings and a radome ahead of being fitted with the prototype sensors for the Integrated Sensing and Non-Kinetic Effects & Integrated Communications System (ISANKE & ICS).