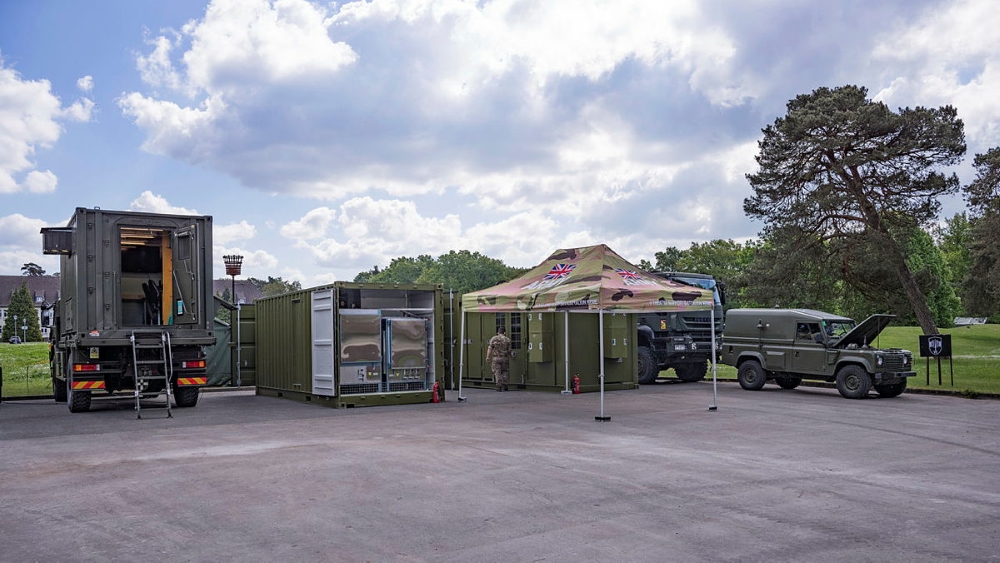
Babcock has announced its delivery of a package of proposals for parts that could be produced through additive manufacturing (3D printing) in support of a number of defence systems in use across the Armed Forces.
The components identified are used on the L118 Light Gun, on the 4.5 inch naval gun found on Type 23 frigates (and Type 45 destroyers) and in the torpedo launching system used on the ASTUTE-class SSNs and the incoming DREADNOUGHT-class SSBNs.
From these proposals, the MOD’s Defence Equipment & Sypport (DE&S) has already picked the Light Gun’s eye shaft, recommending it for adoption in the defence inventory. Babcock is ready to have it ordered through its Material Availability Service. This development represent a new, significant step forward for Project TAMPA, a 7-year frame work that the MOD has established with the firms Babcock, NP Aerospace, RBSL, Thales and AMFG to explore and mature ways in which additive manufacturing can help support equipment in the field, transforming material availability across defence operations. Deployable Additive Manufacturing has been a topic of interest for DE&S in Abbey Wood since 2018, but the program stepped up its ambitions following a discussion on the topic with the US Marine Corps in the city of Tampa, which ended up giving the project its name.
The MOD was encouraged by the USMC’s own vision of agreeing with vehicle manufactures a design library of components that can be created through additive manufacturing, so that spare parts can be literally created in place even on the remotest Island of the Pacific, lessening the strain on the logistics train.
The UK Strategic Command and DE&S’s Future Capability Group thus set up the discussion with key suppliers involved in delivering and supporting the UK’s own vehicle fleets. The main problems to be tackled in order to make the vision viable were identified in a lack of system to securely transfer print files; Intellectual Property or Design Rights; certification and qualification of parts to ensure they’d be fit for use and robust inventory management.
These are the central tenets of Project TAMPA and have shaped the project since 2022. Within the Framework, capability is being developed in Spirals, the first of which aims to produce and fit fit metallic non-safety critical parts with Thales, Babcock, AMFG, NP Aerospace and RBSL engaged in the process. Before Babcock, NP Aerospace and RBSL had already secured approval for a number of parts to be used on Mastiff, Ridgback and even Challenger 3.
NP Aerospace, working in partnership with DMC, demonstrated it can rapidly produce parts for the rear step and door latch assemblies for the British Army’s Mastiff and Ridgback vehicles. TAMPA’s second Spiral steps up in ambition and looks at safety-critical parts. The urgent need to support Ukraine in the war against the Russian invasion has led to priority being accorded to solutions for the Air Domain and to parts relevant to support of platforms granted in kind to Kiev. Alongside the main Spirals, the Future Capability Innovation delivery team is supporting other advanced manufacturing challenges in Defence and looking at how the holistic MOD spare-part availability and supply chain obsolescence can be improved. Obsolescent components in Land Rover Wolf jeeps and other older platforms have been identified for 3D printing, solving difficulties in procuring them through other channels.
Earlier this year, the British Army registered a first by deploying a large scale in-field design and 3D-printing capability to produce spare parts during NATO exercise STEADFAST DEFENDER. It was the first such instance at scale in a NATO event. 9 Theatre Support Battalion, Royal Electrical & Mechanical Engineers deployed metal and plastic 3D-printing equipment in containers moved on trucks. One container hosts a laboratory for the design phase, one has the 3D printers and another is used for post-print treatments.
The 3D printing technology works by using computer-aided design to digitally produce a component. Fine metal powders, such as copper, aluminium, or steel, are fired through a nozzle at three times the speed of sound as a mechanical arm shapes the component, building the object one layer at a time. Once constructed, the component is then subjected to post-processing such as heat treating, milling, and finishing. The aim is to be able to receive designs for parts directly from the homeland and have a deployed capability to make changes or adjustments or create new designs before printing the parts directly in the field.
While in this first instance the parts being produced were mostly for the humble Land Rover WOLF, in future the parts will be used across even the high-end armoured vehicle fleets including AJAX and CHALLENGER 3.